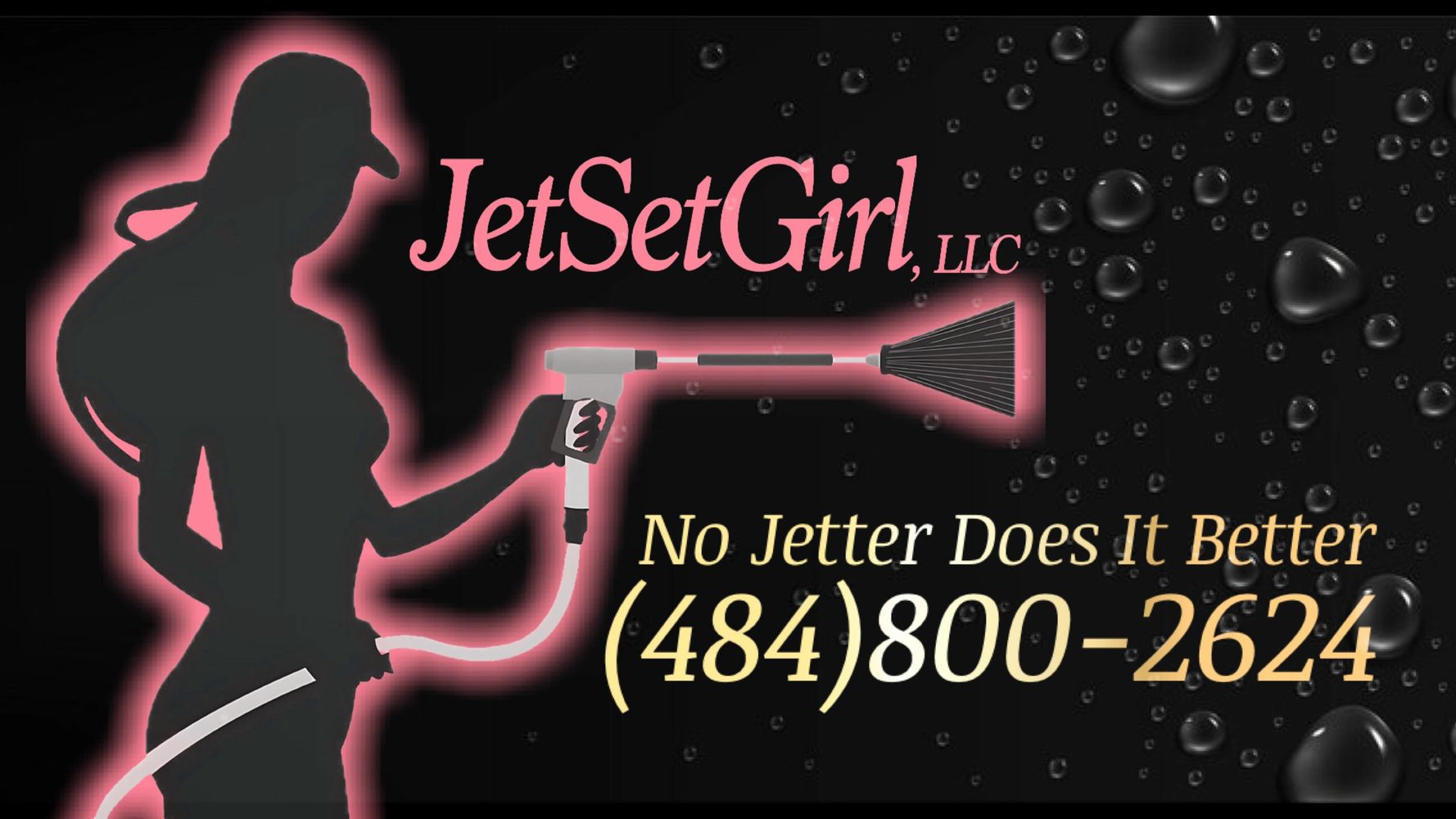
SPECIALIZING in
Commercial & Residential Hydro Jetting
*No Jetter Does It Better*
> Commercial Kitchen Exhaust Hood System
>Drainage Systems/Laundromats
> House Vinyl Siding Cleaning
*No Jetter Does It Better*
> Commercial Kitchen Exhaust Hood System
>Drainage Systems/Laundromats
> House Vinyl Siding Cleaning
Our team of professionals brings over 20 years of experience in hydro jetting, making us experts in the field. We possess the skills and knowledge to tackle any job, whether it’s a minor issue or a major project. We specialize in unclogging drainage pipes and thoroughly cleaning industrial kitchen exhaust systems. No matter the size or complexity of the task, we’re equipped to deliver exceptional results, ensuring your systems operate smoothly and efficiently. Trust JetSetGirl, LLC to handle your toughest challenges with precision and care.
At JetSetGirl, LLC, we are committed to delivering the best possible results for our customers by using only top-of-the-line equipment. Our powerful and efficient machines ensure that every job is done to the highest standard. Our team utilizes advanced, high-precision camera systems to accurately locate and diagnose clogged drains, providing you with a clear visual inspection. When it comes to cleaning restaurant exhaust systems, our commercial-grade pressure washers are unmatched, effectively tackling even the toughest grease.
We specialize in jetting services, including hydro jetting for clogged drains. For laundromats, we ensure that drains are clear of what we refer to as “Goo”—a buildup that, if left unchecked, can cause unpleasant odors reminiscent of sewage when opening a washer. This buildup can also lead to blockages, resulting in flooding. Keeping your drains clean is crucial, and we offer free video inspections so you can see the exact issue and understand what you’re paying for.
In addition to drain cleaning, we provide top-tier cleaning services for restaurant kitchen exhaust systems. We hold ourselves to the highest standards, ensuring that your exhaust system, including the hood, duct, and fans, is thoroughly cleaned to look brand new. We also take pride in our meticulous cleanup after every job, including next-day roof cleaning.
No Jetter Does It Better
1. Comprehensive Grease Removal:
We meticulously clean the entire exhaust hood, including the interior surfaces, filters, fan, and ductwork. Grease buildup poses a major fire hazard and can compromise air quality in the kitchen. We use specialized degreasers and high-pressure hot water to dissolve and remove all grease deposits, leaving the hood pristine and safe.
2. Filter Cleaning:
While we do not replace filters, we ensure that all existing filters are thoroughly cleaned. Our team carefully removes and cleans each filter, eliminating any grease and debris to restore proper airflow and efficiency to the exhaust system.
3. Exhaust Fan and Motor Cleaning:
We clean the exhaust fan, including the blades, motor, and housing. This step prevents grease buildup that can cause motor strain or failure, ensuring the fan operates at its full capacity. Clean fan components are crucial for optimal ventilation and reducing fire risk.
4. Ductwork Cleaning:
We access and clean the entire duct system connected to the exhaust hood. Often, grease accumulates in the ductwork, which can be a hidden fire hazard. Our technicians use specialized tools such as jetters, brushes, scrapers, and high-powered vacuums to thoroughly clean the ducts, ensuring no grease is left behind.
5. We Don’t Cut Corners:
Safety is our top priority. Cutting corners in exhaust hood cleaning can leave behind hidden grease deposits, creating a dangerous fire risk. We commit to thorough, detailed cleaning in compliance with NFPA 96 fire code standards. Our technicians are trained to use the most effective cleaning methods, ensuring every nook and cranny is properly addressed.
6. Detailed Inspection and Reporting:
After cleaning, we conduct a full inspection of the exhaust system to check for any damage or potential issues. We provide you with a detailed report outlining the condition of your system, the areas cleaned, and any recommendations for further maintenance.
7. Scheduled Maintenance:
To maintain a safe kitchen environment, regular cleaning is essential. We offer tailored maintenance schedules based on your kitchen’s needs, helping you keep the exhaust system in peak condition and compliant with safety regulations.
Why We Never Cut Corners:
Proper kitchen exhaust hood cleaning is critical for fire prevention. Grease buildup in the hood, fan, and ductwork can ignite and spread rapidly, putting lives and property at risk. We ensure that every component is cleaned to eliminate potential hazards. Cutting corners is not an option when safety is on the line.
1. Visible Grease Build-Up: The most obvious sign is grease residue left on the surfaces of the ductwork or fan blades. Proper cleaning should result in a shiny, grease-free surface, but cutting corners leaves behind patches of grime and sticky residue.
2. Missed Hard-to-Reach Areas: Cutting corners often means neglecting areas that are harder to access, like the deep interior of ducts, bends, or the back of fan blades. These spots may still be coated in grease, posing a fire hazard and affecting airflow.
3. Unpleasant Odors: An incomplete cleaning job allows grease and debris to accumulate and decompose, which can emit strong, unpleasant odors throughout the kitchen.
4. Poor Airflow: The fan may not function optimally if blades are left greasy or if the ducts are not fully cleared of debris, resulting in reduced airflow and increased heat and smoke in the kitchen.
5. Residual Smoke or Smoke Stains: If the system hasn’t been properly cleaned, smoke stains may remain on the interior surfaces, indicating grease build-up that could affect kitchen air quality.
6. Increased Noise: A fan system that hasn’t been cleaned thoroughly may operate louder due to the extra strain from grease-coated components, indicating it wasn’t cleaned or maintained correctly.
Proper, thorough cleaning should leave the fan and duct system free of grease, with clear airflow and no unpleasant odors or residue. Cutting corners in this process compromises both safety and efficiency.
Our professional jetting service for laundromat washer drainage systems ensures that your drains remain clear of clogs, buildup, and blockages. Laundromat washers often deal with large amounts of lint, detergent, fabric softener residues, and other debris, leading to slow drainage, backflows, and operational disruptions. Our specialized jetting process and inspection methods address these issues thoroughly to keep your laundromat running smoothly.
1. High-Pressure Water Jetting:
We use high-powered, industrial-grade jetting equipment to deliver a strong stream of water into the drain lines. This process effectively breaks up and flushes out accumulated debris, including lint, soap scum, grease, and mineral deposits, without damaging the pipes.
2. Sewer Camera Inspection:
Before and after the jetting process, we use a specialized sewer camera to inspect the drains. This allows us to identify the exact location of blockages and assess the condition of the pipes. By visually inspecting the drainage system, we can ensure that the jetting has thoroughly cleared out all debris and provide you with peace of mind.
3. Clearing Blockages:
Our jetting service targets stubborn clogs that can cause water to back up into washing machines. With the aid of the sewer camera, we can pinpoint problem areas and use high-pressure water jets to clear them out, restoring full drainage capacity.
4. Preventative Maintenance:
Regular jetting, combined with camera inspections, is a crucial part of laundromat maintenance. This proactive approach not only clears existing blockages but also helps prevent future issues by thoroughly cleaning and monitoring the condition of the drain lines.
5. Thorough Inspection:
During the jetting process, our technicians use the sewer camera to inspect for potential issues, such as damaged pipes or areas prone to buildup. We provide detailed feedback and recommendations for ongoing maintenance, helping to prolong the life of your drainage system.
6. We Don’t Cut Corners:
We understand how crucial a fully functional drainage system is for your laundromat’s operations. Cutting corners in drain cleaning or inspection can lead to missed blockages or undetected issues. Our combination of jetting and camera inspection ensures a comprehensive clean, reducing the risk of future problems and costly emergencies.
By choosing our jetting and inspection service, you can trust that your laundromat’s washer drainage systems will be clear, efficient, and ready to handle the demands of daily operation.
After pressure washed
We love our customers, so feel free to contact us.
Philadelphia, Pennsylvania 19114, United States
Open today | 07:00 am – 05:00 pm |
If you have reached us after hours, please send us an email and we will contact you back as soon as possible
We are excited to offer a 25% discount on our jetting services for commercial kitchens! To take advantage of this offer, please review the following details:
How to Qualify:
1. Sign a Non-Binding Contract – Commit to a scheduled jetting service frequency for one year.
2. Provide a Credit Card on File – A valid credit card must be kept on file for billing.
3. Service Exclusion – The 25% discount does not apply to the first-time Hydro Jetting service.
Discount Terms & Conditions:
• The 25% discount applies only to services starting from the second visit, after signing the contract.
• The discount is not retroactive and cannot be applied to any services prior to contract signing.
• The first-time Hydro Jetting service is excluded from this discount.
• A valid credit card must remain on file for the duration of the agreement.
We use cookies to analyze website traffic and optimize your website experience. By accepting our use of cookies, your data will be aggregated with all other user data.